Industrial and Automotive MIM Applications
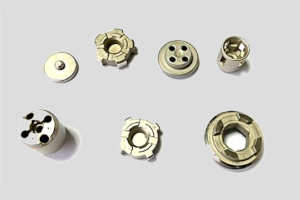
trending_up Automotive Applications
MIM components for motor vehicles
- Body and chassis parts
- Steering system parts (lock caps and bolts)
- Seat and seat belt parts (locking pawl)
- Oil pump parts and nozzles
- Valve system parts
- Engine: turbocharger parts (Turbine Vane and Wheel)
- Adjusting rings
- Engine: Pump and Injector
- Interior and other parts
- Engineļ¼ FIP & Nozzle
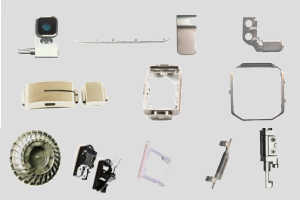
trending_up Communication and Electronics
Computer, Communication and Consumer Electronics
- headphone decoration phone parts
- side key phone parts
- internal structure phone parts
- charging interface parts
- SIM Tray/SD parts
- CPU Cam Parts
- Computer spindle parts
- Fan components
- Return caps
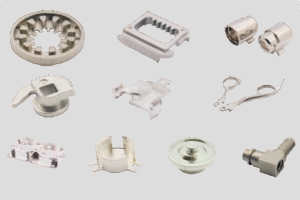
trending_up healthcare and tools
Medical & Healthcare & Power tools
- Minimally invasive surgical devices
- Cardiac instruments
- Pacemakers
- Dental implants
- Cardiac instruments
- Small levers
- Small housings
- Small hings
- Small plates
- Connecting rods, Push Rods, Stop Rods
- Gears and Facegears
- Skides and Screws
- Shifting Guide Plates
Automotive MIM application fields
MIM products are used in many places in motor vehicles
Primary and secondary levers, housings and other lever type are typical components of the valve system.
For Engine-Turbochargers turbine valves and wheels and also adjusting rings available by MIM technology.
The FIP and nozzle system contains many MIM parts (Injector & Sealing Seats, Lower and upper anchor, Polo piece, IV DISC, OCV seat, Sealing plugs, Vanes, Pistons, Check Plates, OCV stop, Disc check plate).
For seat systems and seat belt systems hinges and plates, locking pawl, connecting rods, seat control with valve plates and valve springs are typical MIM parts.
For the stearing system normally lock bolts and lock caps will be made by MIM technology.
For the car body and chassis gears and facegears, slides and screws, return caps, push rods and shift guide plates made by MIM technology.
Many use cases for car interiors exist like speed adjusting rods, blocks, stop rods, core stonel Sol lever, locking hubs and other locking mechanism, magnetic core Stonel SOL, Thumb wheels.
Metal Injection Molding (MIM) Process Steps
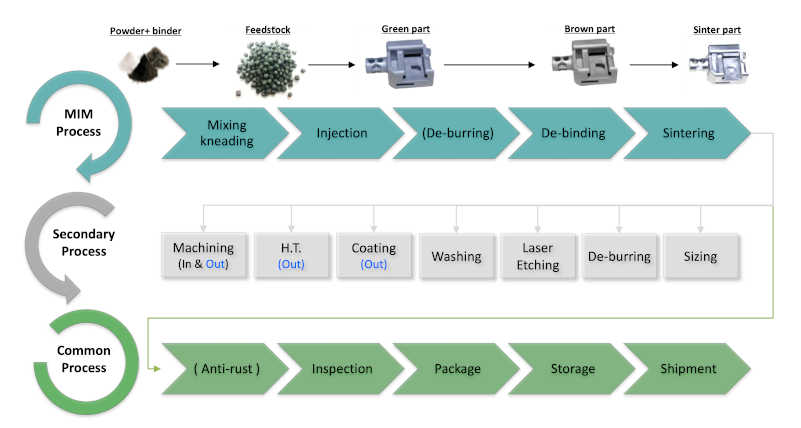
metal injection molding
Process Flow
Metal Injection Molding Characteristics
Metal injection molding sometimes also called powder injection molding is a multi step process where a powder is mixed with binder materials to form a feedstock that will be injected in the mold cavity to form a green part.
The so called brown part is created by the de-binding process, that removes all the binder material from the formed part.
The final sinter process is responsible for creating the final material attributes.
Especially in the field of healthcare medical requirements for minimal porosity and part cleanliness can be ensured.
Metal Injection Molding (MIM) is a net-shape process. As a result, you have great freedom in the design of components that still have the corresponding strength values in the end.
This also applies to requirements for the part density, since large porisities under the surface, which are often assumed, can be prevented by different process steps in the MIM process
Compared to cast parts with subsequent CNC processing, the MIM process can achieve significant cost advantages
In the past few years, the raw materials for the MIM process have continued to improve. The part properties can be achieved in a very targeted manner with a wide variety of alloy variants
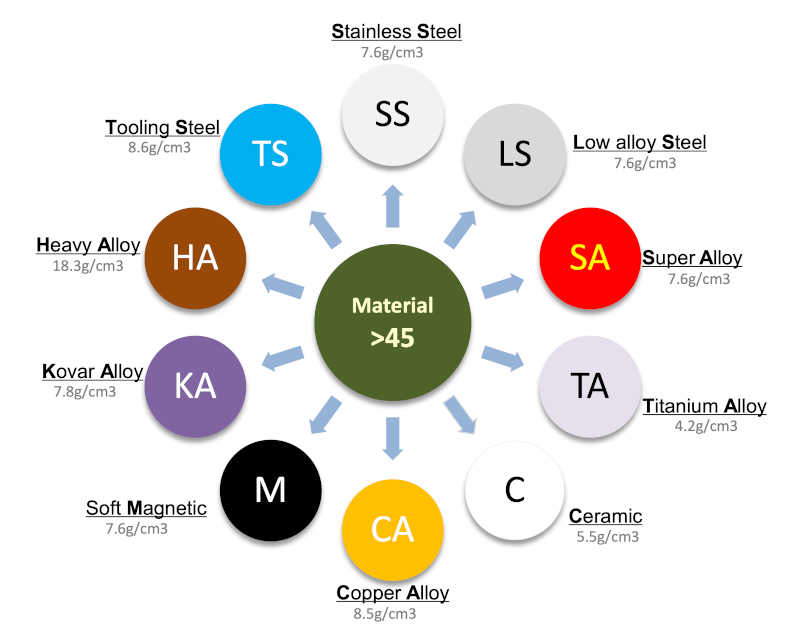
metal injection molding
Material composition
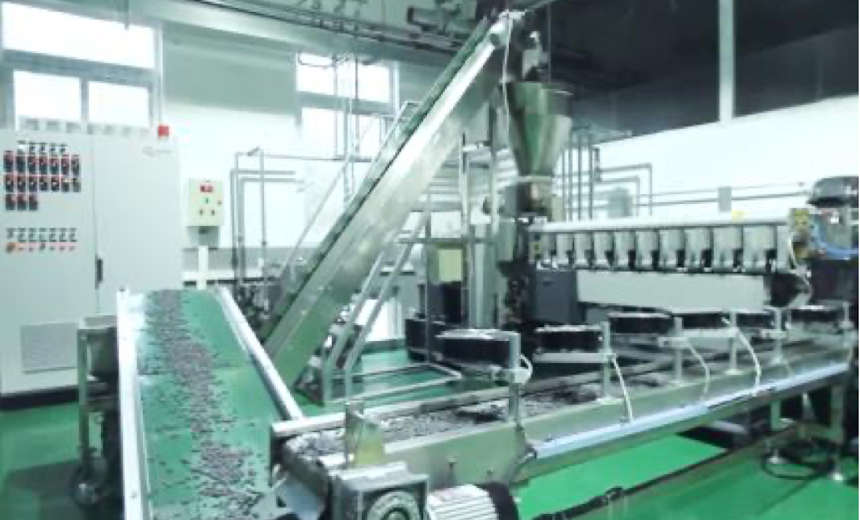
MIM Feedstock-Machine
Preparation of the raw material for injection molding
Metal powder in an alloy composition is mixed with a special binder and thus forms the raw material of the MIM process
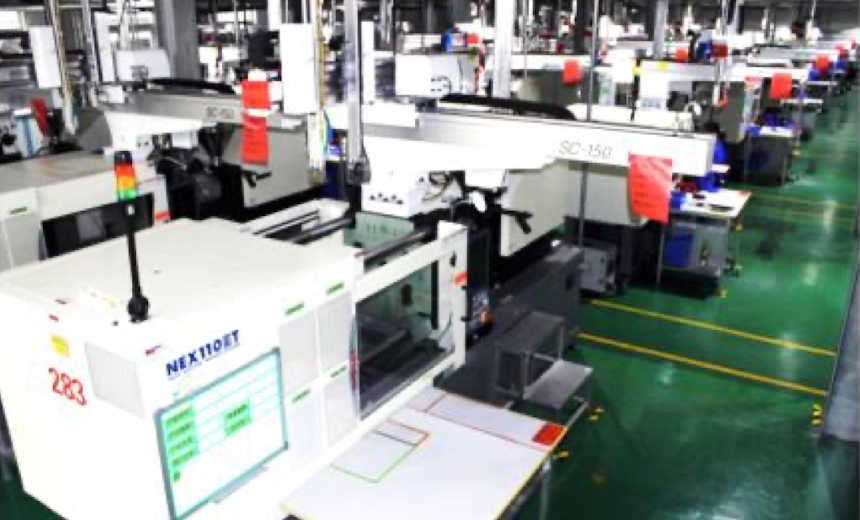
MIM Injection-Machine
The shaping metal injection process step
The feedstock is injected in a liquefied form (usually at an elevated temperature) into a closed mold, where it fills the mold (cavity) completely and then plastifies it through targeted temperature control.
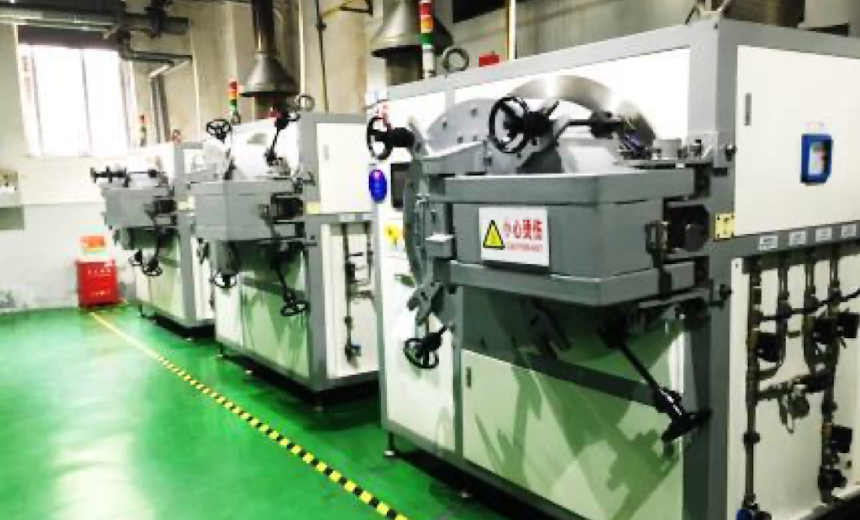
MIM De-Binding-Furnace
After the shaping has been completed, the binder must be removed
After the green part has been removed from the injection molding machine, the binder is removed again in a two-stage process, the debinding. A purely metallic or ceramic component is created.
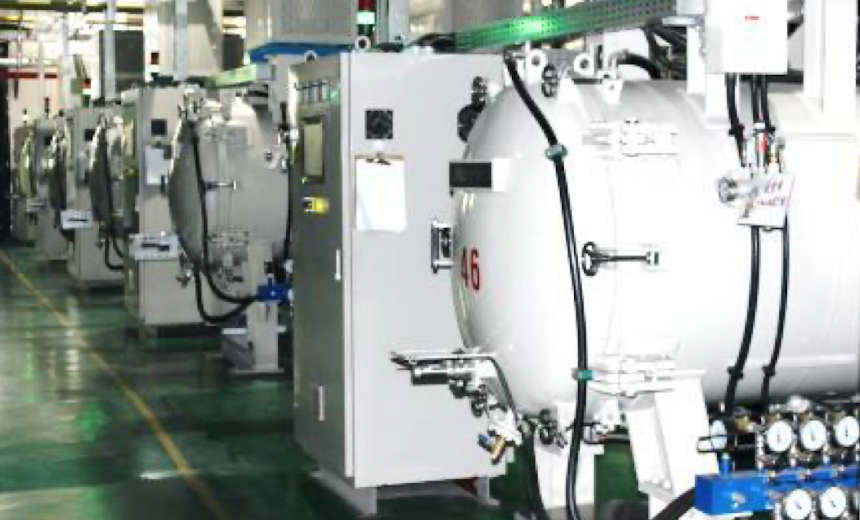
MIM Vacuum-Furnace
Allow for excellent control of the debinding and sintering process
The porous molded body that remains after debinding, now called the brown part, is compressed to a component with its final geometric and mechanical properties by sintering at high temperature.
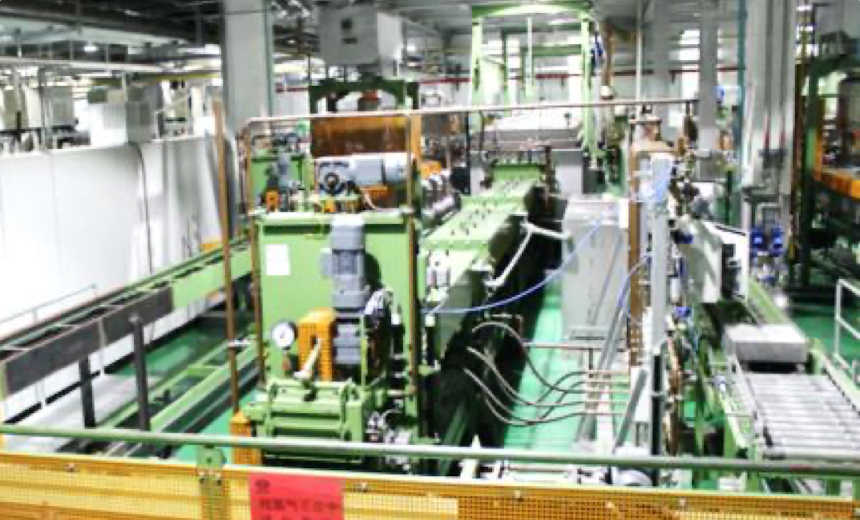
MIM Continuous Furnace
Continuous furnaces entail vital advantages opposite to chamber or batch furnaces
For MIM production, it is important to know that the parts respond very sensitively to vibration during residual debinding and sintering. Therefore, parts or charge boats must be low- vibration carried.
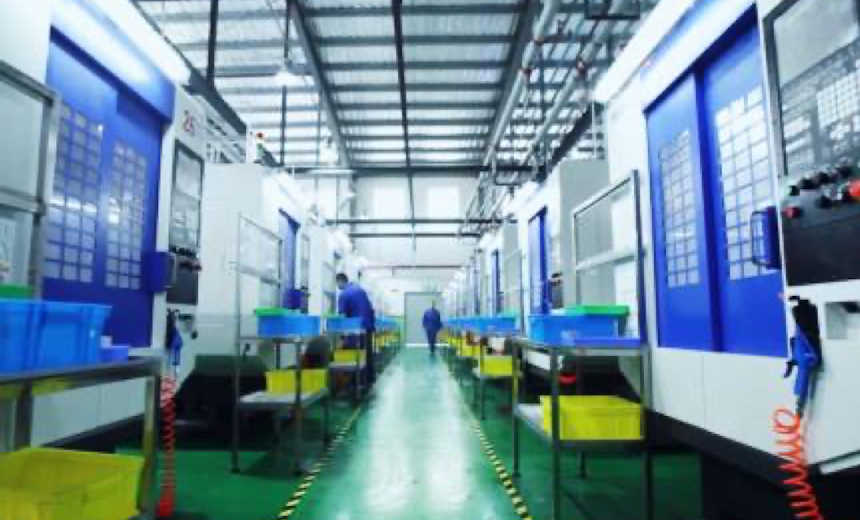
MIN CNC-Machining-Center
Reach the final tolerances
In certain cases, the tolerances and surface accuracies that can be achieved with the MIM process are not sufficient and CNC post-processing must be carried out.